10 Lean Six Sigma Red Flags
Don’t let these red flags overwhelm your LSS Program
Over the past 20 years TMAC has provided training and support for dozens of different LSS deployments, across a variety of industries. During that time, our staff have provided over 5,000 hours of project coaching for Green Belts and Black Belts.
As we meet with each belt our staff listen closely for anything which is cause for concern. We would like to share some of the ‘Red Flags’ encountered over the years during these coaching sessions. TMAC’s role during coaching is to not only identify such Red Flags, but also to provide guidance on how to overcome them.
In the table below the Red Flags are prioritized based on occurrences. These findings apply to both Green and Black Belt projects, and for any type of business. The only other consideration is that these Red Flags are focused on Project Issues. In a future blog we will discuss Red Flags which are Program Issues.
Now, what exactly do we mean by ‘Red Flags’?
These are issues or concerns which can have a negative impact on the success of a project. Often the impact is in the form of higher project costs or longer project timeframes. Sometimes the impact manifests itself as rework for belts or team members. Other times the problem can be the wrong tool was used or the right tool was used incorrectly. In a worst-case scenario, the Red Flag will greatly increase the likelihood of project failure.
The more Red Flags we see, the more we know that company’s LSS Program is struggling. And to achieve its potential there must be active countermeasures to address these project risks.
The good news is these Red Flags are not insurmountable. There are proven methods to overcome them – you just have to know where to start and be willing to do the hard work necessary for project success. Don’t let these challenges overwhelm your LSS Program.
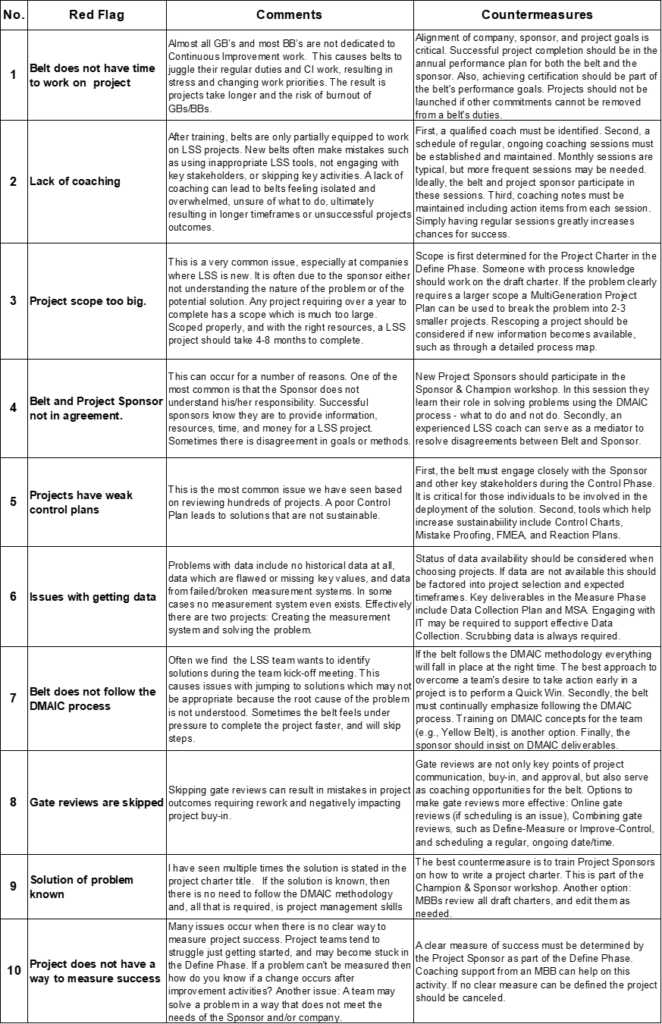