The Power of Scientific Thinking in an AI World by Conrad Soltero
Artificial Intelligence, Cybersecurity, Additive Manufacturing – it’s a brave new world. Business leaders are focused on high tech and emerging markets. Innovation and automation seem to be the name of the game. Does that mean if your company is not “in” any of these trends, you’ll soon be “out” of business? Perhaps AI and robotics will indeed replace many workers in the coming years. One proven defense to the increasing pace of technological change: Scientific Thinking.
Scientific Thinking has long been a mainstay of problem-solving and innovation. For those working in Continuous Improvement both DMAIC (quantitative) and PDCA (qualitative) are commonly used scientific modes of thinking. However, both of those improvement methods are commonly associated with project-based improvements, such as kaizen events. This results in better process performance over time – but only when a project occurs as shown below (project improvements are shown as vertical green arrows):
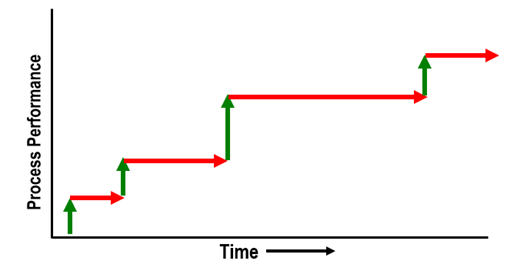
There is one big assumption with the graphic shown above: Once an improvement occurs the process is stable and maintains the new, improved performance level until the next kaizen event or DMAIC project. Unfortunately, in most cases this is not what happens. It is much more common for process performance to stagnate – or deteriorate – between improvement projects. This results in a process performance graph which looks something like this:
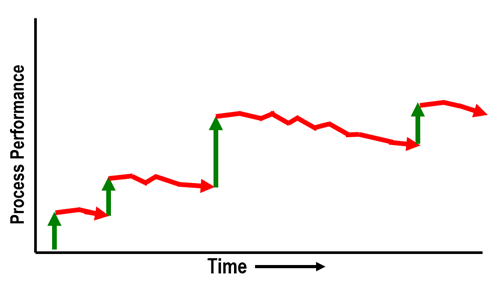
Is there a way to ‘lock in’ the improvements so this gradual degradation does not occur? Also – is there a way to make simple and gradual improvements between improvement events? That is, to make incremental improvements on a day-to-day basis? Can Scientific Thinking play a role in how workers perform their daily tasks? And what does Scientific Thinking have to say about fostering better human relationships?
The answer is absolutely! In this blog we will explore how Scientific Thinking applied through 1-on-1 methods can result in highly productive teams of human beings who use their creativity to (a) sustain consistent process performance and (b) solve incremental business problems on a daily basis. No AI required!
Before going further, I’d like to emphasize the importance of standards. Taiichi Ohno, the Father of the Toyota Production System, once said, “Without standards, there can be no improvement.” He was right, of course. As shown in the two graphs when standards are established then improvements can be sustained. But without standards improvements tend to fade away. Of course, LSS practitioners know the Control Phase of the DMAIC process is all about the use of standards to sustain solutions. Bottom line: Standardization comes first.
What is the best approach for accomplishing this? Training Within Industry. TWI is a time-tested, simple, but effective methodology for implementing Scientific Thinking among workers and supervisors on a day-to-day basis. Developed during World War II, TWI was instrumental in ramping up production of materiel to support the war effort. Even more impressive, it was implemented using individuals not commonly part of the workforce at that time (remember Rosie the Riveter?). TWI has since been adapted for use all over the world, in both manufacturing and service settings. In essence, TWI gives supervisors the skills to apply Scientific Thinking in their daily activities with direct reports.
The starting point with TWI is Job Instruction (JI). It is the perfect tool for teaching workers how to perform their jobs correctly, the first time, in a straightforward manner. It provides the mechanism to sustain improvements.
Optimally, JI begins with the standard training for supervisors which any qualified TWI instructor can provide. This training should be followed up with an additional JI workshop which teaches supervisors how to both analyze and properly document a specific task. Lastly, organizations should begin development of TWI-JI coaching skills throughout the supervisor ranks.
There are four objectives to a successful Job Instruction program:
- Standard method for instruction
- Proper analysis of a task
- Proper documentation of a task so it is conducive to one-on-one training
- Development of coaching skills
Now to be clear, the JI program applies the use of PDCA in teaching a task. So Scientific Thinking is embedded into this learning model.
But what if the learner is obstinate and puts forth little effort in learning? Or even worse, what if two workers understand their roles but just can’t seem to get along. The JI program does not provide a solution for these situations. But another TWI program – Job Relations (JR) – does. JR is tailor-made to handle human relations dilemmas. And it uses Scientific Thinking as a basis for solving human problems when they do arise.
The JR program picks up where the JI program leaves off. It provides preventive as well as reactive methods for the improvement of human relations. The preventive portion of the program provides a set of foundations for minimizing risk of human relations problems. These preventive measures, however, cannot be readily integrated into behavior. Rather, the JR program seeks to develop a supervisor’s ability to mentor once coaching has been learned from the JI program.
The skill of coaching provides the practitioner with an ability to provide constructive criticism to the learner. Mentoring takes the next step by enhancing coaching through the introduction of interactive communication. More succinctly, coaching is about pointing out mistakes and correcting them. Mentoring occurs when the mentee (the learner) asks for expertise and opinion from the mentor. So – Coaching tends to be one-way communications (from the Coach to the Worker) whereas Mentoring is inherently two-way communications (back and forth between the two).
In essence, the TWI JI and JR courses provide a script for the application of Scientific Thinking via PDCA which can be practiced and improved upon. These two programs provide supervisors with powerful and valuable skills for the development of highly productive human teams.
In next month’s blog, we will explore a powerful and proven method for continuous improvement to make incremental improvements between projects: The Toyota Kata.