Customer Spotlight: Will McDade, Interstate Batteries
This month’s newsletter is one in a series about individuals working in continuous improvement. Each LSS practitioner gets to share their journey in CI and some lessons learned. This month I spoke with Will McDade. Over the course of his career, he’s led Continuous Improvement initiatives at three different companies: Amerimax, Dr Pepper, and Interstate Batteries. He completed his LSS Black Belt training with TMAC in 2004 and was certified in 2005. Recently he retired after ten years as CFO and COO at Interstate Batteries.
Your background is in accounting. Can you talk a little about your early career. What were some of your first job assignments? What areas did you work in before becoming involved in Continuous Improvement?
My first role at Dr Pepper in 2000 was to consolidate the accounting for multiple divisions and systems. During a hiatus from Dr Pepper in 2004-2005 I was in charge of plant accounting at Amerimax Building Products, a supplier of quality products for the Recreational Vehicle, Manufactured Housing and Modular Building industries. That is when they asked me to get involved with Continuous Improvement and sent me for my Black Belt.
How and when did you first get involved in CI?
When I was at Amerimax Building Products, our President asked me to enhance my role as Cost Accounting Manager by getting trained as a Lean Six Sigma Black Belt in 2004. I used a yield improvement project at our Arkansas Paint Line plant to save almost $250K per month in scrap. I was able to transition into full-time CI role at that point and also had the opportunity to help turn around a plant in Indiana for almost a year.
What was your initial reaction when you first learned about Lean Six Sigma?
I knew that the Black Belt training would be a game changer for my career. I didn’t want to be an accountant for the rest of my career, I wanted to be more involved in leading the business. The training was difficult and very comprehensive, but I knew all the studying would be worth it.
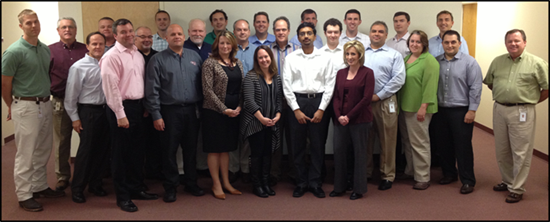
Tell me about your LSS training. What did you like? Dislike?
We trained at UTARI in Fort Worth and the trainers made it a lot of fun. Each one of us brought a project to work on and got to also hear the other trainees’ projects which were very diverse and interesting. I also liked having multiple trainers that each had different expertise. Many of the concepts were new and foreign to me (one piece flow, WIP) and many were difficult statistical concepts (Multiple regression, ANOVA) but the teachers made much it easier to understand. My class invented ice cream day which made it much more fun!
Can you share a little about your experience as a Black Belt leading project teams?
The key to leading project teams is not to be the “smartest one in the room”. Most of the good ideas come from the people that do the job every day, not the Black Belt. You need the team to feel like they own the project, not the Black Belt.
What did you like best about working as a BB?
I liked the unique challenges and projects and not doing the same thing every day. The feeling of accomplishment from improving a process and seeing the results is very rewarding.
After leaving Amerimax in 2005 you went back to work for Dr Pepper. As I recall, the Continuous Improvement Program there went through different phases. Can you talk about your role, and how the CI program changed over time?
After receiving my Black Belt while at Amerimax, I was recruited by one of my mentors, the EVP of Operations, to go back to Dr Pepper and help lead manufacturing and supply chain. At DP I was in many different roles in both supply chain and finance. My Lean principles allowed me to reduce waste and cost in each role. My final role at DP was to start up and lead the Rapid Continuous Improvement (RCI) group which improved our free cash flow by $250 million and more than tripled our stock price in about 4 years.
When I was initially leading CI as part of my manufacturing role, we really focused on doing drawn out DMAIC projects in the plants. The lack of speed made it challenging to deliver significant results and was frustrating at times. When our new CFO came in 2010 he suggested we use the Rapid Continuous Improvement Kaizen methodology similar to what Danaher used and we really took off.
We would basically use a 4-5 day Kaizen with 20-25 team members to do the Analyze and Improve Phase and use a smaller team for the pre-work and follow-up. We had a staff of around 40 Lean Six Sigma professionals that facilitated 3-4 Kaizens per week. Each Kaizen was 4-5 days all across North America and was focused on delivering results of $500K+ each. We would start with a large opportunity and use breakout groups, each facilitiated by a Black Belt, to tackle individual opportunities within the Kaizen. The CEO and his direct reports attended the kaizen event report outs every Friday morning from 9am-noon. Shop floor workers, drivers, and entry level office employees would be presenting the solutions they implemented to the CEO, CFO, and President each week! The finance team tracked these savings for a year and we actually publicly reported the savings to Wall St. (you can Google it).

Then you moved to Interstate Batteries in 2015. At that point you moved into an executive role. How did your background in LSS affect your decision-making?
Right, my experience at DP led to my CFO and COO roles at Interstate Batteries where I applied similar principles to focus on improving free cash flow with breakthrough team-member led change. The first person I hired at IB was someone to help me implement Continuous Improvement. The first project we worked on was reducing month-end close time in accounting from 45 days down to about 15 or so. This really helped set the tone for the rest of the organization. We then set breakthrough goals for each area of finance and then the whole business and rewarded team members for achieving them. That is how Interstate still operates, and that first hire is still at Interstate running a big part of their supply chain
Looking back, how did Lean Six Sigma affect your career?
My career would have been very different without my LSS training. I would probably be in accounting or maybe FP&A at a much different level in my career. Learning to lead through employee-led change and Kaizen set my experience apart from others in my field.
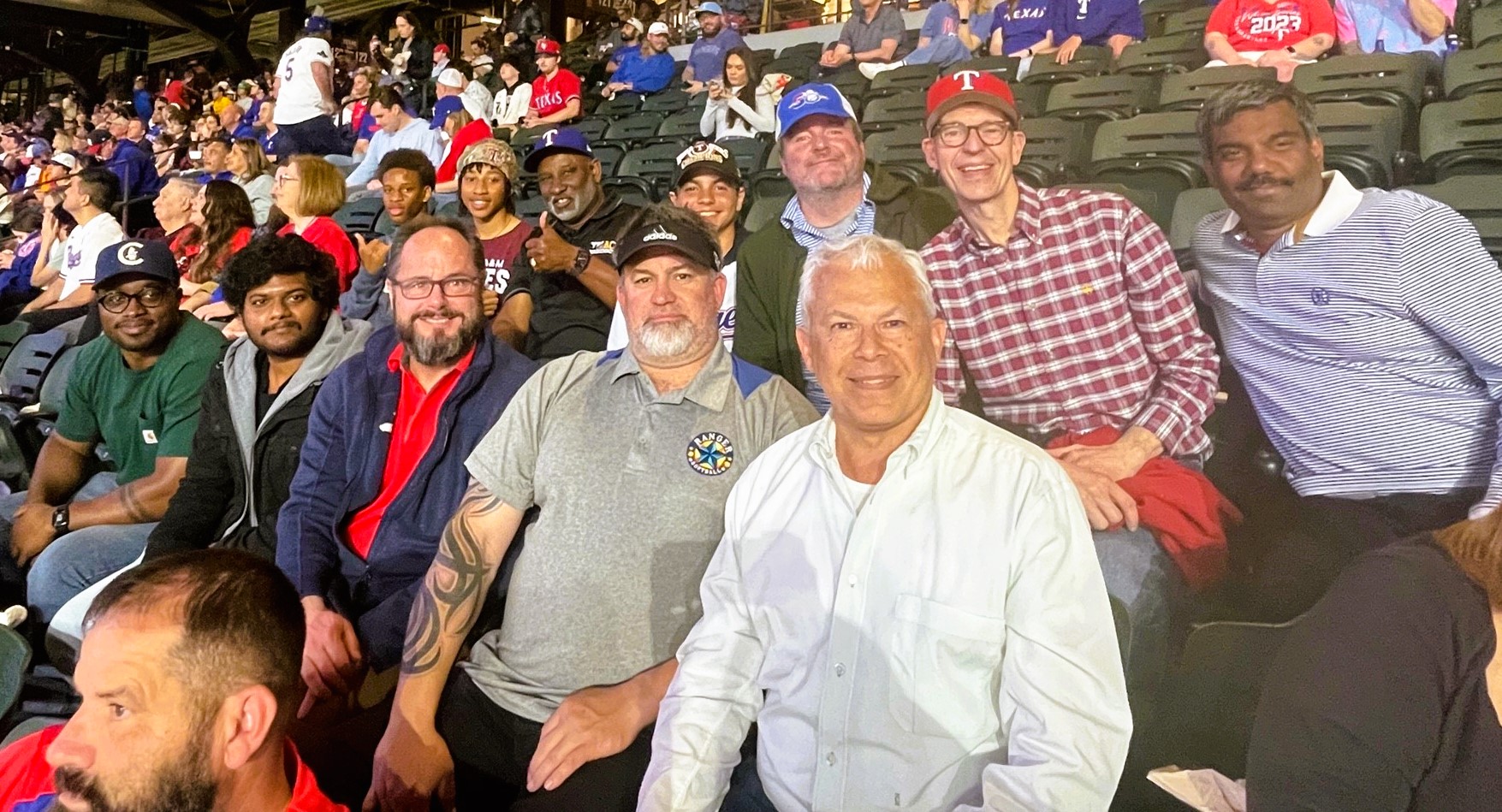