Customer Spotlight: Ryan Johnson, CoorsTek
This month’s newsletter is one in a series about individuals working in continuous improvement. Each LSS practitioner gets to share their journey in CI and some lessons learned. This month I spoke with Ryan Johnson, a LSS Black Belt with CoorsTek, a privately owned manufacturer of technical ceramics for aerospace, automotive, chemical, electronics, medical, metallurgical, oil and gas, semiconductor and many other industries. Ryan completed his BB training with TMAC in 2022.
When did you begin working at CoorsTek, and what was your role? What other areas did you work in before becoming involved in Continuous Improvement?
I began my career with another ceramics manufacturing company where I started as a process engineer. Exposure to CI as a young engineer was critical to becoming an effective team member and ultimately earning a leadership role. Executing various LSS projects introduced me to each of the core business functions and helped me build the knowledge I needed to take on a role in operations management.
In that role I was able to help the company organize critical product lines into value streams and assign the equipment, operations and engineering resources required to support each. This experience helped prepare me for my current role at CoorsTek where I started in 2022. As a global process engineer, I work to deploy structured problem-solving tools with local engineering teams and lead Black Belt projects (primarily DMAIC format) across the organization.
Note: I read an influential book while entering my first operations role, “The Goal” by Eliyahu M. Goldratt. Bit dated but the principles explored hold up!
How and when did you first get involved in CI?
Within my first year as an engineer, I was given the opportunity to pursue a LSS Green Belt. The company ran an internal training program, hosted at an offsite property with lodging, allowing employees to leave behind daily responsibility and focus entirely on the learning process. After a couple of weeks at “LSS Camp” I was eager to return to our processes and view them through a new lens!
What was your initial reaction when you first learned about Lean Six Sigma?
I quickly embraced LSS because I loved its foundation in data-driven decision making. As a young engineer, building a narrative with data was the best way I could capture the attention of my colleagues and bolster support for the solutions I proposed. It also brought reassurance that I was on the right track. In other words, did the change I piloted make a statistically significant difference in the KPI?
I also came to understand how helpful Lean Six Sigma can be in broadening perspective when approaching a problem. To answer all the questions required to start an LSS project, you can’t help but look at the bigger picture. What is the VOC? What are the KPIs? What is the problem, really? Where is the waste? And not only are you inspired to ask these critical questions, LSS also offers a complementary toolset for discovering the answers. For example, Pareto Analysis to determine the most impactful failure mode with a yield problem or Value Stream Mapping to identify the rate limit step in a throughput problem.
There was a particular moment in my belt training where the power of approaching a problem with a broadened perspective became apparent. We were organized into small teams and asked to complete a challenge. The challenge was to improve the performance of a drag racing pit crew. This was simulated by team members taking on different pit crew roles and sending a K’nex toy drag racer to one end of the room and back. The pit process was documented, essentially replacing the k’nex wheels and rubber band “engine”, but you could see TIM WOODS (the 8 wastes of Lean) everywhere.
Eager, we got right to work applying SMED (single minute exchange of die) principles and picking apart each process step. The result was a substantially better race time, but we were still short of the course record. It was then that we realized that in our excitement we had failed to define the problem statement and really understand the VOC. When we took this step back it occurred to us that the car only had to make it to the other end of the room and back, and there were no restrictions preventing us from changing the design of the car. In an epiphany it became apparent that the car could be built with two engines allowing one rubber band “engine” for each leg of the race and essentially eliminating the entire pit crew process / all downtime.
Tell me about your LSS training. What did you like? Dislike?
What I appreciated the most about the Black Belt course was the opportunity to build my knowledge of applied statistics. The instructors very clearly introduced the topics, and we worked through several case studies as a class. This built familiarity and made applying statistical tools more approachable. Also helpful was allowing time to discuss each belt’s project and the unique tools being applied in their application. In addition, I found instructors and peers to be very insightful when we presented these BB project updates to the class.
Can you share a little about your experience as a Black Belt leading project teams?
Fortunately, CoorsTek has a long history of LSS culture and local teams are very receptive to initiating Black Belt projects. The projects themselves, however, are quite challenging as the scope often spans several production facilities. Working on complex products that have operations across multiple facilities means working with many people/processes at once. To make it even more complicated, symptoms appearing in one process can often be traced to root causes in another process which could be at facilities in another part of the country or the world.
What did you like best about working as a BB? Biggest lessons learned?
CoorsTek has a diverse materials portfolio is a global company. What I enjoy most about being in this role is constantly learning about new materials, processes, places and meeting a lot of great people along the way. I also appreciate that the solution to a Black Belt project doesn’t often lie in any one person or data set. We work in multifunctional teams and must learn from each other to understand the problem and deliver a solution. Everyone has something to contribute.
And what was most challenging?
The greatest challenge has been establishing good measurement systems. These are critical to forming an accurate baseline and ultimately coming to a solution. Unfortunately, measurement system and baseline development take time, especially with products that have long cycles of learning.
Tell me about your career path since your first assignment as a BB. And what would you like to do in the future?
The successful completion of my first BB project, supported by TMAC, definitely advanced my career. Since that time, I’ve been fortunate to have been assigned to work with some of CoorsTek’s top customers and in our largest business segment. No matter what challenge I’ve been faced with LSS has taught me to see the whole picture and given me a toolset to come to a solution.
From here I’d like to continue to grow my understanding of structured problem solving. One of the ways in which I’m planning to do this is taking the MBB course through TMAC this fall. With this I can see myself continuing to develop in my role, coming to manage a team of BBs or perhaps exploring a commercial role where I could combine understanding of VOC with technical knowledge.
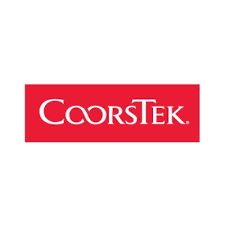