Customer Spotlight: Kellie Foglio, USG Corporation
This month’s newsletter starts the first in an occasional series about individuals working in continuous improvement. Our goal is to let LSS practitioners tell their stories and share some lessons learned. This month I spoke with Kellie Foglio, a LSS Master Black Belt with USG Corporation.
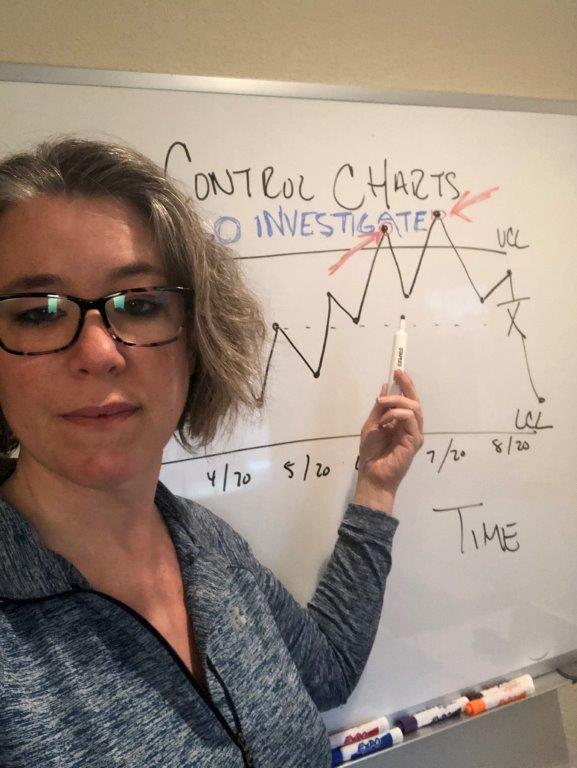
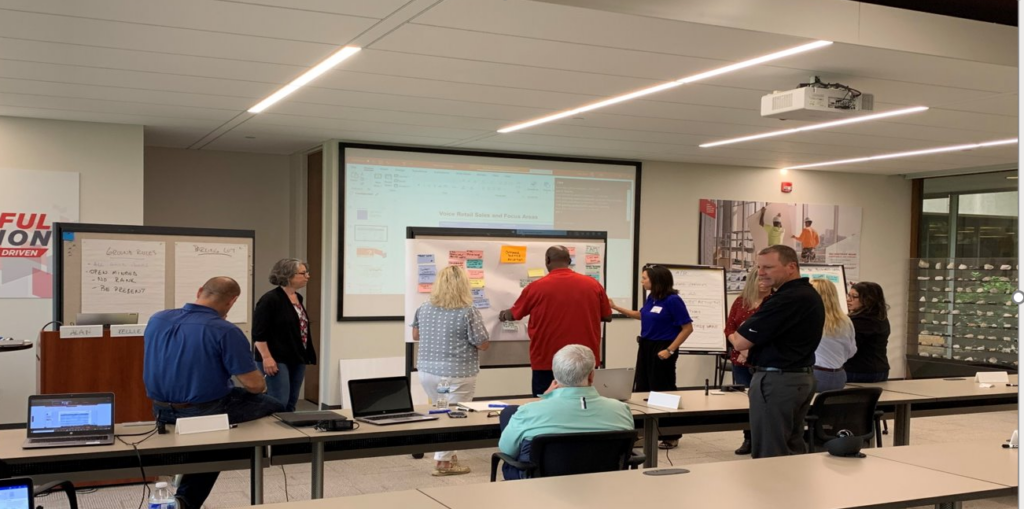
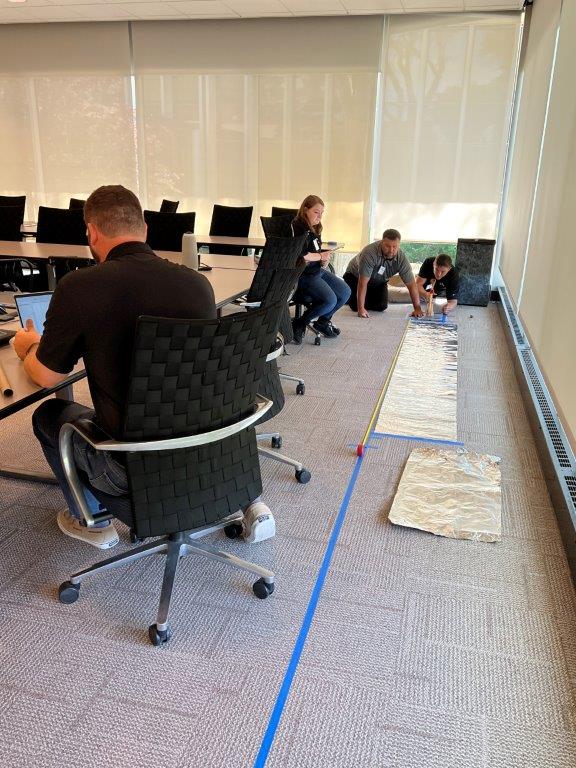
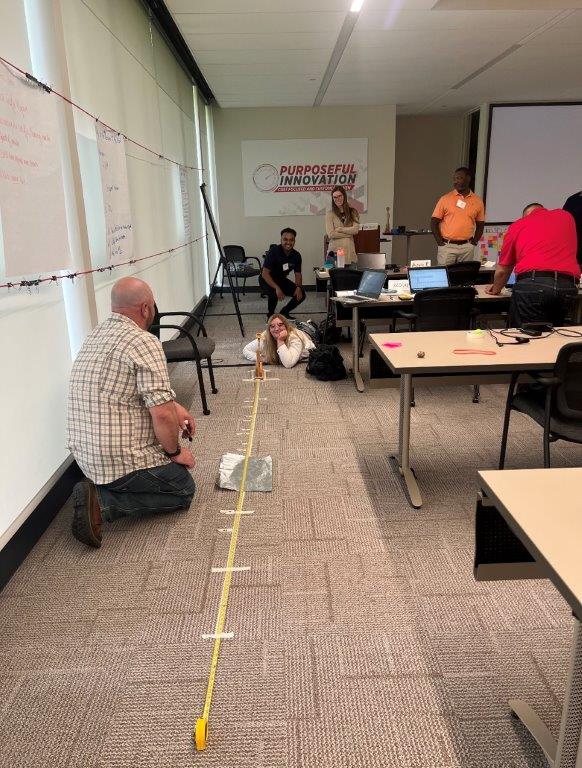
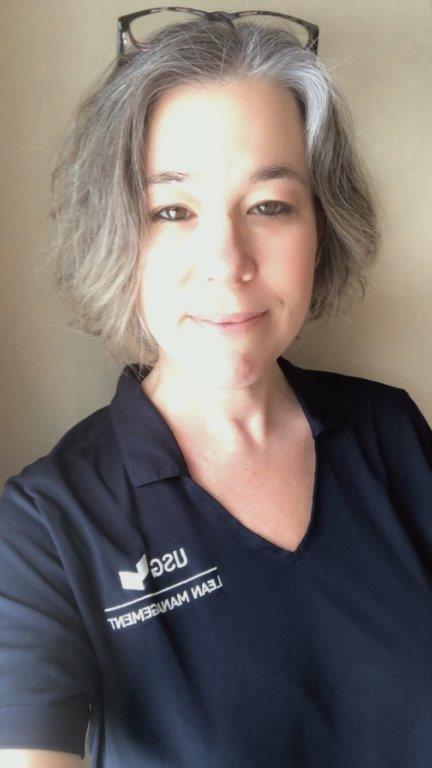
- When did you begin working at USG Corporation, and what was your role?
- My educational background is biology, with a focus on biochemistry and statistics. I joined USG in 1999, and started in research & development in Libertyville, IL. My job duties included new product development, formulation work in our lab, product QC, quality customer response, test development, technical writing, bulletin/standard work development, and research reports.
- How and when did you first get involved in LSS?
- I’ve been exposed to the tools throughout my career from gage work in the lab, the importance of standards, regression, and DOE including mixture design. Our R&D group often brought in experts from places like Minitab or Univ. of Illinois to develop staff. In fact, in 2013 U of I came in to offer a Design for Six Sigma class which I attended. This is when my career opportunity with LSS came up. We already had a LSS Program deployment in Operations. That program had earned enough trust and interest to begin a Corporate Deployment. The LSS Program Champion at the time, James Wilson, visited our DFSS class. Apparently, my high interest and excitement in the DFSS class prompted the instructor to recommend me to James. At the same time, I reached out to a mentor of mine, then head of Research, and got plenty of encouragement. I took the leap from R&D to help develop the new Corporate Deployment.
- What was your initial reaction to LSS / DMAIC concepts?
- I absolutely LOVED that it was based in customer focus. My heroes throughout my career were big advocates of doing right by the customer: Heads of Quality, Legal, R&D and my first MBB. It’s a blend of my favorite things. Removing waste or nonsense that holds no value for the customer and is often painful for the worker or to cost. The encouragement of questioning WHY we do things and investigation through testing makes the scientist in me very happy. The ability to make data driven decisions… It all clicked. More than anything, the utilizing of teams to get to the best answer is brilliant.
- Tell me about your LSS training.
- It started with TMAC’s LSS Black Belt course which I attended in the Summer of 2013 along with four coworkers. After working as a BB for about a year I came back for Master Black Belt training. That class began in June 2014 and was also with TMAC. USG also had onsite training on DMEDI/DFLSS by TMAC in 2014. I’ve attended other workshops and classes on continuous improvement topics over the years including the DFSS class through U of I, Minitab training on DOE, Mixture Design, and Gage R&R.
- Can you share a little about your experience leading project teams.
- The coolest was my first project about reducing cycle time for an approval process for chemicals and materials to be used in plants. It was vital that we kept true to our core principle of safety while also recognizing there was a lot of unnecessary waste in the process. To deliver innovation to our customers, efficiency and speed in proper piloting from bench to full scale is critical. This approval process was a constraint that needed to be resolved.
- It was a diverse team with staff from legal, plants, researchers, environmental and analytical labs. Once we got everything mapped…and it covered a huge wall… we all stood back and said, “I had no idea you did that. WHY?” All the rework loops, waiting, overprocessing was shocking. It essentially was a broken process that needed an overhaul to focus on what was really value add. So that’s exactly what we did. The project took longer than expected, but we went from a mean of 129 days to 13 days and a median of 43 days down to only 5, all while keeping safety the main focus. The biggest thing I learned about project management was from Brian Christ, my coach at the time: Trust the process.
- What did you like best about working as a BB?
- The best was not having to have the answer. It was freeing. In my previous experience as a project manager I felt like I had to have all the answers. Not so with LSS. My team knew they were selected because they were the experts. My role was to ask questions and facilitate tool use. Also, we set up pilots so any failure could be identified before the full-scale launch occurred. We were all learning.
- And what was most challenging?
- Diverse personalities. Managing a tenured, experienced team with strong bias and assumptions was really challenging. They all were protecting their own siloed territory. There was a lot of seeking to understand that really pulled the team together. In the end, the process they built was highly advocated by them. As influencers, that buy-in was critical to sustainability of the solution.
- What has your experience been like as an MBB?
- Project work: I’ve led several META [very large scope] projects. They have varied from ones working with suppliers on the team to ones focused directly on customer. They always span many plants or functional teams.
- Coaching: My coaching has been very diverse. I have had belts from manufacturing, IT, supply chain, customer service, R&D, marketing, engineering, tech service, finance, sales, and more. I’ve also done some coaching in Lean events as our company has rolled out Lean Management. I like the diversity of exposure. Coaching is a critical piece of the puzzle. You can’t learn concepts in class and just stick that binder up on a shelf and expect success. We invest in each belt on a weekly basis and often more if needed. They know we are in it with them. Most belts would struggle a lot without regular coaching.
- Teaching: I have led our belt program for several years and it’s really where my passion lies. I’ve taught 20 of our GB classes, starting back in 2014. We are always working to improve modules, simulations, and really take the feedback from our belts to heart. A confession – I was TERRIFIED of public speaking and it came through “on stage.” The stuff that would make you get sick or faint. Bad. During my MBB class with TMAC we had to do practice teaching. Russ spotted me coaching a coworker through a Minitab exercise. He pulled me aside and said “Just do that rather than present a topic.” When it came time for my practice teaching on multiple regression, I turned off the slide deck and asked the class to open up Minitab and we dove right in. Great advice that sticks with me to this day. Thanks Russ. I no longer present but teach. I also offer this coaching to belts nervous about leading a team.
- What do you like best about working as an MBB? What is most challenging?
- Best: Teaching, hands down. LOVE IT. The moment where eyes light up and they get it. Students are inspired and feel like they can make all the difference. They tie one tool to the next during training and also learn how to manage team dynamics. We host a whole extra week on team facilitation/soft skills before they dive in to LSS and stats-y stuff. I’ve heard several say this was the best week of their career. It certainly was the best week of mine.
- Most Challenging: Seeing belts not get the resources or backing from their managers. This will kill a highly engaged belt and team.
- How has LSS affected your career path?
- After leaving research as a BB, I fast tracked into my MBB role in less than a year. I’m in the best job. I know at this point I should have jumped back into the business, but I really do love what I do. There hasn’t been an alternative that has piqued my interest since. Not only that, I have the best co-workers. We truly are a team and our strength comes from building off each other. My peers are the reason this is so enjoyable.